In alle aandacht voor hergebruik van consumentenproducten lijken we een enorme afvalstroom over het hoofd te zien: autobanden. Als het gaat om hoogwaardig recyclaat uit afgedankt rubber is het nog steeds pionieren. ‘Er is nog veel onbekendheid met dit onderwerp.’
Een onzichtbare berg, zo zou je onze jaarlijkse stroom aan uitgerangeerde autobanden wel kunnen noemen. Dat ligt overigens niet aan de omvang. ‘Alleen al in Nederland hebben we het over zo’n tien miljoen afgedankte autobanden per jaar. Dat is nogal wat’, zegt Geert Heideman, associate lector kunststoftechnologie bij Hogeschool Windesheim in Zwolle. Storten en verbranden zijn, zeker wereldwijd gezien, de meest gangbare route voor oude banden. Een beetje hergebruik is er wel, maar het blijft marginaal. ‘Recycling is voor de bandenindustrie niet nieuw’, zegt Wilma Dierkes, associate professor Sustainable Elastomer Systems/Elastomer Technology and Engineering en mede-oprichter van het Elastomer Competence Centre aan de Universiteit Twente. Ze werkte zelf ooit bij bandenfabrikant Vredestein. ‘Dertig jaar geleden waren we daar ook al actief met recyclaat om bij te mengen bij nieuw rubber, maar het ging toen en het gaat nog steeds om lage gehaltes.’
Een andere toepassing van vermalen oud rubber is als steunlaag onder kunstgrasvelden, maar dat is omstreden vanwege het mogelijk vrijkomen van schadelijke stoffen. Los daarvan is het ook weer een voorbeeld van downgrading, dat we vaak zien bij het recyclen van kunststoffen. Je kunt met het recyclaat wel iets, maar de toevoegde waarde is twijfelachtig. Het is meer uitstel van het uiteindelijke verbrandingsproces dan serieus herwinnen van waardevolle grondstoffen.
Eric Roetman: ‘We willen de waarde van het rubber behouden’
Wangen
Het grote probleem is dat banden, net als heel veel andere producten, uit meerdere componenten én materialen bestaan. Bij een band heeft bijvoorbeeld het loopvlak een andere samenstelling dan de ‘wangen’, de zijkanten van de band. Loopvlak en wangen bestaan uit rubber, maar niet uit dezelfde soort rubber en bovendien vaak uit blends; mengsels van meerdere typen rubber. En dan zijn er nog heel andere materialen. Staal voor de stevigheid, textiel voor versterking en vulstoffen zoals roet en silica. Heideman somt het even op: ‘Een band bestaat al snel uit acht verschillende compounds die elk wel tot twintig additieven bevatten. Ook de structuur is complex, het is niet een massief blok rubber, maar het zijn verschillende lagen op elkaar.’ Gooi je een band dus gewoon in de vermaler — zoals dat nu gebeurt — dan hou je een behoorlijk ongedefinieerde brij over waar je weinig meer mee kunt.
Maar met betere sortering en scheiding vooraf en goed afgestemde chemische processen voor herwinning van het gebruikte rubber, moet de kwaliteit van het recyclaat enorm op te krikken zijn, zo is de overtuiging van onderzoekers bij het Lectoraat Kunststoftechnologie en het Elastomer Competence Centre. Beide instellingen werken daarom al enige tijd intensief samen om de recycling van banden naar een hoger niveau te tillen. ‘Onze insteek is dat we beter recyclaat kunnen leveren als we beter gedifferentieerd startmateriaal hebben. We willen de waarde van het rubber behouden’, zegt Eric Roetman, onderzoeker bij het Lectoraat Kunststoftechnologie en tevens promovendus bij de TU Delft. Volgens Geert Heideman kun je met beter recyclaat serieus meters maken. ‘In de rubberindustrie gaat tachtig procent van de productie naar banden. Als je het gehalte aan bijgemengd recyclaat kunt opkrikken, maak je echt winst.’
Dat begint bij dus bij het efficiënt sorteren en uit elkaar halen van gebruikte autobanden. Maar waar moet je echt op scheiden? Heideman: ‘Het type rubber is een belangrijke factor. Bij banden van personenauto’s bestaat het loopvlak meestal uit een SBR/BR blend [styreen-butadieenrubber / butadieenrubber, red.], terwijl de wangen vaak meer natuurrubber bevatten. Dat is belangrijk om gescheiden te houden.’ Naast het rubber zijn ook de vulstoffen een cruciale component. Loopvlakken bevatten roet of silica; te verschillend om bij elkaar te gooien. Bovendien gaat het om flinke gehaltes. In de rubberwereld werkt men met PHR, parts per hundred rubber, als eenheid en voor vulstoffen heb je het dan al snel over gehaltes van 60. ‘Dat is echt wel meer dan een pigmentje’, merkt Heineman droogjes op.
Wilma Dierkes: ‘Het materiaal wordt nooit beter dan waar je mee begint’
Voor de rest van de additieven zijn de gehaltes minder cruciaal, maar daarbij speelt iets anders. Het is namelijk lang niet altijd duidelijk wat er precies in een band zit. Binnen de EU zijn milieulabels op banden vereist en die geven wel enig inzicht in de samenstelling, maar toen Roetman onlangs een inventarisatie maakte kwam hij op het duizelingwekkende aantal van 155.000 verschillende typen banden. ‘Maar we weten niet in hoeverre die banden echt van elkaar verschillen op een manier die uitmaakt voor ons proces. En dan zit je nog met banden van buiten de EU, vooral uit China, en daarvan weet je niet precies wat erin zit en de merknamen veranderen ook de hele tijd. Hoe moet je dan goed sorteren?’
Ontwerpgericht onderzoek
Dat dit een probleem is zie je meteen als je nadenkt over een efficiënt sorteringsproces. Idealiter zit er daar een stap in waarbij het label op de band automatisch wordt gelezen, waarna de band in de juiste categorie wordt geplaatst voor verdere verwerking. Maar met zoveel typen banden en markeringen op de banden die bovendien niet alles onthullen is dat nogal een uitdaging. En dat is niet de enige. Want je hebt bijvoorbeeld ook systemen nodig die de banden efficiënt uit elkaar halen en de verschillende lagen rubber scheiden. Toch zijn het precies die uitdagingen waar ze bij het lectoraat hun tanden inzetten. Heideman: ‘Het uiteindelijke doel is om een pilot lijn te bouwen waar je echte, afgedankte banden in stopt en dan kijkt welke stromen je kunt genereren. Dat vraagt heel veel stappen om over na te denken en te ontwikkelen.’ Bedenken, ontwerpen en bouwen - die combinatie is belangrijk. Roetman: ‘Wij doen hier met de studenten ontwerpgericht onderzoek en dan loop je tegen heel veel praktische zaken aan als je dingen ook echt moet gaan ontwerpen en bouwen.’
Devulkanisatie
Laten we aannemen dan het in de toekomst mogelijk is om uit een bonte collectie afgedankte banden, redelijk uniforme materiaalstromen te genereren. Dan moet je nog steeds van oud, gebruikt rubber terug naar de grondstoffen. Even snel opfrissen: rubber is een netwerk van onderling verbonden polymeerketens. Die crosslinks komen tot stand tijdens het vulkaniseren: door het toevoegen van zwavel en zwavelverbindingen aan de ruwe grondstoffen, ontstaan op de plaats van dubbele bindingen in de ketens zwavelbruggen tussen de losse ketens en krijg je een elastisch, maar tegelijkertijd stevig netwerk.
Wil je dus van oud rubber terug naar het startpunt, dan moeten die zwavelbruggen weer worden verbroken, en dan is precies wat Wilma Dierkes en haar team doen. Voor hen is devulkanisatie de voorkeurstechniek om hoogwaardig recyclaat te maken. Die techniek wordt al wel gebruikt, maar vooral voor vrachtwagenbanden. Dierkes: ‘Bij vrachtwagenbanden is het heel gebruikelijk om het loopvlak te vervangen, waardoor je daar al een behoorlijk uniforme stroom materiaal voor recycling hebt. Bovendien bestaan vrachtwagenbanden voornamelijk uit natuurrubber en dat is makkelijker te devulkaniseren en weer te gebruiken dan de synthetische rubbers in banden van personenauto’s. Natuurrubber bevat naast zwavelbruggen nog allerlei eiwitten die ook een rol spelen bij de netwerkvorming, ook na devulkanisatie. Dat zorgt ervoor dat je weer een goed, nieuw netwerk kunt vormen.’
Eric Roetman: ‘Er zijn meer goede redenen om rubber te recyclen dan alleen CO2 reductie’
Vernetting
De groep van Dierkes zoekt naar hulpstoffen om de devulkanisatie van synthetische rubbers te verbeteren. ‘Het gaat om de verhouding tussen de hoeveelheid verbroken S-S bindingen en verbroken polymeerketens. Hoe hoger die ratio, hoe meer je het netwerk ontkoppelt, zonder dat je kortere ketens krijgt.’ Toch gaan we niet naar 100% recyclaat als grondstof voor nieuwe banden, zegt Dierkes. ‘Nee, dat gaat niet. Je werkt met verouderd materiaal en het wordt nooit beter dan waar je mee begint.’ Om zo gericht mogelijk te devulkaniseren, gebruik je ook weer zwavelverbindingen. ‘Onze insteek is om te werken met zwavelverbindingen die al worden gebruikt bij de productie van rubber, waaronder een zwavelhoudende weekmaker. Deze verbindingen splitsen in twee radicalen en die ‘pakken’ dan de uiteinden van een zwavelbrug, waardoor die breekt. Naast deze hulpstoffen spelen ook de temperatuur en de afschuifkrachten een rol, daarmee kun je het devulkanisatieproces ook beïnvloeden.’
Omdat je bij devulkaniseren weer reactieve uiteinden opwekt is het essentieel om het proces op tijd te stoppen. Dierkes: ‘Bij SBR moet je daar echt goed op letten, want je krijgt heel snel een ongecontroleerd vernettingsproces dat blijft doorgaan.’ En dan heb je dus weer vast rubber in plaats van je gewenste recyclaat. Voor ieder type rubber is daarom een specifiek afgestemd proces nodig. Wat zijn volgens haar de belangrijkste parameters om het oude rubber op te scheiden en sorteren? ‘In ieder geval het polymeer zelf, welk type rubber is het? Ook de verhouding tussen de materialen in blends is belangrijk, net als de gebruikte vulstoffen. En het type netwerk. De dichtheid en lengte van de crosslinks zijn ook belangrijk. Hoe langer de crosslinks, hoe makkelijker ze te verbreken zijn.’ Op basis van haar onderzoek weet Dierkes dat de gehaltes aan recyclaat in nieuw rubber flink omhoog kunnen. ‘Je kunt 15 tot 20 procent devulkanisaat bijmengen in bepaalde onderdelen van banden.’ Dat zou al een enorme sprong zijn vergeleken met de huidige situatie. En misschien met steeds beter recyclaat, kunnen die gehaltes nog verder omhoog.
Kip-ei
Wat is er nodig om oud rubber op veel grotere schaal in te zetten als hoogwaardige materiaalstroom? Daar zijn Dierkes, Heineman en Roetman het roerend over eens: opschalen op alle fronten. Zowel het sorteren en scheiden als het devulkaniseren. Bij Windesheim hebben ze al een werkende opstelling, op basis van het Twentse onderzoek, om op kleine schaal rubber te devulkaniseren met extruders. ‘We zijn echt nog aan het pionieren’, zegt Roetman.
Dat is eigenlijk verbazingwekkend als je bedenkt hoe lang het al gaat over de circulaire economie en de noodzaak van minder afval, minder energieverbruik en meer recycling. Zeker in vergelijking met bijvoorbeeld de aandacht die uitgaat naar recycling van alle plastics. Zo’n rubberberg zou je toch moeten zien liggen? ‘De financiering van dit soort onderzoek was lange tijd heel lastig, omdat rubber niet viel onder het begrip kunststoffen als het om recycling ging’, zegt Heideman. ‘Dat is gelukkig veranderd, rubber is nu wel meegenomen in Duurzame Materialen NL dat vanuit het Nationaal Groeifonds wordt gefinancierd.’ Dat plasticrecycling meer aandacht krijgt verbaast hem niet. ‘Dat is technisch veel makkelijker en je hebt sneller resultaat als je kijkt naar CO2 reductie. Niet zo gek dat men daar graag mee wil scoren.’
Geert Heideman: ‘Je moet de moeilijke problemen niet tot het laatst uitstellen’
Toch is die nauwe focus op CO2 niet zinvol, zegt Roetman. ‘Er zijn veel meer goede redenen om rubber te recyclen. Denk aan de afhankelijkheid van grondstoffen.’ Maar moeten we om het gebruik van recyclaat op te schroeven niet gewoon naar wettelijke eisen voor fabrikanten? ‘Fabrikanten zijn terughoudend, omdat ze bang zijn voor aansprakelijkheid bij schade die mogelijk aan het gebruik van recyclaat te wijten is’, zegt Dierkes. ‘Maar fabrikanten moeten meer hun best doen en daarvoor moet de wetgever de druk opvoeren. Daar ligt een probleem vanwege de onbekendheid met dit onderwerp. De wetgever ziet te weinig dat hier een kans ligt, dat bewustzijn ontbreekt nog.’ Toch is dit ook niet zo eenvoudig, denkt Roetman. ‘Dat is toch een kip-ei vraag. Wat heb je eerst nodig? Regelgeving of techniek? Het heeft geen zin om regelgeving te maken zonder dat je de techniek hebt, maar zonder techniek komt die regelgeving er meestal ook niet.’
Wat we volgens Heideman in ieder geval niet moeten doen is afwachten en uitstellen. ‘Je moet niet de lastigste problemen tot het laatst bewaren, omdat het nu misschien iets minder CO2 reductie oplevert dan andere onderwerpen. Als we in 2050 circulair willen zijn moet je niet pas tegen die tijd beginnen hiermee. Juist omdat het lastig is, moet je er de tijd voor nemen. We moeten het toch een keer oplossen.’
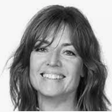
Nog geen opmerkingen