Kevlar, Dyneema, Twaron, Vectran, Zylon, Tenax: de wereld van de supervezels staat bol van de hippe merknamen. Daarachter gaat meer dan een halve eeuw chemische innovatie schuil, die zich inmiddels uitstrekt tot koolstofnanovezels en 3D-geprinte kunststoffen.
- Spinnen maakt sterk
- 3D-printen met Kevlar
- Carbon: supervezel uit de oven
- Trekken, rekken, breken
- Supervezelbadkuip
- Computermodel voor supertextiel
- Biologische supervezels
Spinnen maakt sterk
In de supervezelgeschiedenis hebben Nederlandse chemici en bedrijven een belangrijke rol gespeeld. De labs van DSM en Akzo-Nobel droegen sleuteltechnologie bij aan de ontwikkeling van respectievelijk de supervezels Dyneema en Twaron. DSM verkocht dit jaar de Dyneema-fabricage voor €1,4 miljard aan het Amerikaanse bedrijf Avient. Hoewel dat voor de fabriek in Heerlen geen directe gevolgen heeft, voelt het toch als de afsluiting van een stukje Hollandse industriegeschiedenis.
Die geschiedenis begon in het geval van Dyneema met de zoektocht om uit polyethyleen supersterke vezels te spinnen. Dat wil zeggen: de taaie versie van het polymeer, ultra-high-molecular-weight polyethyleen (UHMWPE) met extra lange ketens van meer dan 200.000 koolstofatomen. Om draden te maken van UHMWPE is spinnen vanuit een organisch oplosmiddel de aangewezen route. Het spinproces draait om het aanbrengen van moleculaire oriëntatie in de kronkelende polymeerketens. Netjes ontward en geordend geven de polymeren de vezel supersterkte door de optelsom van op zich zwakke vanderwaalskrachten.
Het aanbrengen van moleculaire oriëntatie is ook de crux bij het maken van vezels met aromatische polyamides (Twaron, Kevlar) en polycyclische polymeren (Zylon). Nieuwe records liggen in het verschiet met het spinnen van vezels uit een oplossing met koolstofnanobuisjes. Met dit materiaal zijn inmiddels experimentele draden gesponnen, die zich qua sterkte kunnen meten met Kevlar. Koolstofsupervezels hebben interessante extra eigenschappen. Ze geleiden stroom bijna net zo goed als koperdraad; je kunt er een ledlamp mee aansluiten op het stopcontact.
3D-printen met Kevlar
‘We doen in onze vakgroep veel onderzoek aan composieten en ontwikkeling van 3D-printen. Ons idee was: als we die twee technieken combineren, kunnen we dan hoogwaardige composieten maken voor kleine, gecompliceerde ontwerpen van enkele tientallen centimeters groot?’, zegt Lode Daelemans, universitair docent bij het Centre for Textile Science and Engineering in de vakgroep Materialen, Textiel en Chemische Technologie (Universiteit Gent). Hij doet onderzoek aan composieten met nanovezels, innovaties rond textiel en membranen en 3D-printen met supervezels. Zo heeft hij dit jaar gepubliceerd over 3D-prints van PET-polyester met daarin aramidevezels (Polymers 14: 298). ‘We zijn begonnen met glas- en koolstofvezel, maar die zijn bros waardoor ze snel breken als je een bochtig ontwerp print. Daarom zijn we verdergegaan met flexibeler Twaron en Zylon. We gebruiken de standaard aramidegarens van Teijin, die bijvoorbeeld ook worden verwerkt in kogelvrije toepassingen. Die vezels laten we continu meelopen met het gesmolten polymeer van de printer. We kunnen zo mooie ontwerpen maken, waarin de vezels netjes zijn verdeeld. In de vezelrichting zijn de mechanische eigenschappen van de 3D-prints goed, maar bij buiging van het materiaal komen de vezels los van de kunststof. Op dit moment is de hechting tussen het polymeer en de supervezels dus nog beperkend. Waarschijnlijk moeten we chemisch gaan ingrijpen om de hechting tussen vezel en polymeermatrix te garanderen. We hebben laten zien dat 3D-printen met supervezels technisch mogelijk is, maar op dat vlak moeten er nog stappen worden gezet.’
Carbon: supervezel uit de oven
Koolstof- of carbonvezel heeft zich sinds het eind van de jaren vijftig geleidelijk ontwikkeld tot een populaire supervezel. Het materiaal heeft namelijk naast een hoge treksterkte – vijfmaal sterker dan staal – en is in dit opzicht vergelijkbaar met organische supervezels als Kevlar. Daarnaast vervormt het nauwelijks, is het lichtgewicht, chemisch inert en bestand tegen hoge temperaturen. Een van de nadelen is de kostprijs: carbonvezel van hoge kwaliteit is duur.
De kostprijs is wel begrijpelijk gezien de grondstof en het energievretende productieproces, wat bestaat uit het stapsgewijs verkolen van organische vezels bij extreem hoge temperatuur. Het startmateriaal is een draad van polyacrylonitril. Dit organische polymeer bevat naast koolstof ook stikstof en waterstof, en die elementen moeten met enig geweld worden weggewerkt, via oxidatie in hete lucht gevolgd door een verblijf in een stikstof gevulde oven bij een temperatuur die oploopt tot 3000°C.
Tijdens deze moleculaire transformatie ontstaat een zwarte vezel die zich in treksterkte kan meten met organische supervezels. Na deze stap volgt een oppervlaktebehandeling en een polymeercoating. De vezels zijn geschikt voor bijvoorbeeld verwerking in een doek, dat met kunsthars tot een paneel kan worden geperst voor het bouwen van een lichtgewicht motorboot, fietsframe, auto-onderdeel of zeiljacht.
Trekken, rekken, breken
In de wereld van supervezels wordt altijd die ene vraag gesteld: wie is de sterkste? Om daarop een objectief antwoord te krijgen, wordt een trekbank gebruikt. Een staafje, plaatje of kabeltje van het te testen materiaal wordt daarin vastgeklemd. Vervolgens trekt de machine het materiaal uit elkaar tot het breekt. Tijdens de trekproef wordt ook de vervorming van het materiaal in kaart gebracht in aanloop naar de breuk. Voor het materiaal sneuvelt zijn er namelijk al allerlei veranderingen te meten, die informatie verschaffen over materiaaleigenschappen, zoals de elasticiteit. Die eigenschap vertelt iets over flexibiliteit, vervorming onder druk en schokbestendigheid in bepaalde toepassingen. Zo is koolstofvezel stijver dan Dyneema of Twaron.
Wie zoekt naar tabellen met materiaaleigenschappen van supervezels ziet dus vaak twee waarden: de elasticiteitsmodulus (E) en de treksterkte, allebei uitgedrukt in mega- of gigapascal. Treksterkte wordt gebruikt om materialen te rangschikken op sterkte. Dat er in de gemeten waarden nogal wat variatie en bandbreedte zit, laat zien dat de testomstandigheden en de precieze samenstelling van het testmateriaal ook van invloed zijn. In deze ranglijst geldt Zylon als de sterkste commercieel verkrijgbare organische supervezel.
Vezel | Treksterkte (GPa) |
---|---|
Dyneema | 2,4 – 3,1 |
Kevlar | 2,2 – 4,1 |
Zylon | 7,3 |
M5 | 2,5 – 5,5 |
Koolstofvezel | 2,5 – 7,1 |
Glasvezel (E-glas) | 2,0 – 3,4 |
Diamant | 2,8 |
Constructiestaal (A36) | 0,55 |
(Bron: bewerking van tabel 1.1 uit Knijnenberg, 2009)
Supervezelbadkuip
In 2022 vierde Teijin het tienjarig jubileum van ’s werelds grootste gevel waarin supervezels zijn verwerkt: ‘de badkuip’ van het Stedelijk Museum Amsterdam. Deze nieuwe vleugel werd in 2012 geopend en meet 100 bij 25 meter. De gladde gevel bestaat uit 185 composietpanelen opgebouwd uit vinylhars-laminaat met daarin twee soorten supervezels: para-aramide (Twaron) en koolstofvezels (Tenax). Onder het kunstvezellaminaat zit een dikke laag warmte-isolatie, bovenop op een witte coating. Volgens Teijin is het voordeel van deze materiaalcombinatie dat kunsthars uitzet als het warm wordt, terwijl de supervezels krimpen. De optelsom daarvan is dat de panelen nauwelijks vervormen als de buitentemperatuur verandert. Verder leent het gladde, witte oppervlak zich voor projecties, onder meer van het logo van Teijin: het bedrijf sponsort het museum sinds 2007.
Computermodel voor supertextiel
In veel industrietakken zijn computermodellen helemaal ingeburgerd om ontwerpen te testen voordat een prototype wordt gemaakt. In de textielsector is dat nog geen gemeengoed, zegt Lode Daelemans (Centre for Textile Science and Engineering, Universiteit Gent). Computermodellen die het gedrag van textiel kunnen doorrekenen onder belasting, vragen namelijk het uiterste qua rekenkracht. ‘Een enkel garen bestaat uit duizenden filamenten, dus voor een textiel loopt dat in de miljarden. Die filamenten kunnen onafhankelijk van elkaar bewegen, terwijl ze rekken en wrijving van elkaar ondervinden. Dat alles bij elkaar opgeteld vraagt veel rekentijd. Tot tien jaar terug was dit soort modelonderzoek gewoon onmogelijk door een gebrek aan computerrekenkracht. En zelfs nu kost het nog een uur voor een klein textieloppervlak.’
Daelemans is tien jaar geleden samen met collega Wim Van Paepegem begonnen met de ontwikkeling van een textielmodel, Virtual Fibre, en dat begint vruchten af te werpen (Composites Science and Technology 207: 108706). ‘We kunnen gedetailleerde berekeningen maken, en de eigenschappen van de vezels en het weefpatroon zijn eenvoudig aan te passen. Het idee erachter is dat je combinaties van vezels en patronen kunt uitproberen, zonder dat je een experimenteel doek van een paar meter hoeft te weven, om experimenten mee te doen. We kunnen bijvoorbeeld de impact op een Kevlar-weefsel modelleren, en vervolgens het weefpatroon veranderen, en het model laten berekenen hoe goed de afremming van een kogel is. Je kunt ook denken aan het combineren van verschillende soorten supervezels in ballistische toepassingen, of gebruik supervezels samen met gewone polymeren in scheepszeilen.’
Biologische supervezels
De mens kan inmiddels fraaie prestaties leveren met vezels op basis van aardoliepolymeren en koolstof, maar moeder natuur wekt nog altijd enige jaloezie. Vooral spinnenzijde heeft bijzondere eigenschappen: een natuurlijk biopolymeer (eiwit), sterk als Kevlar en bovendien tweemaal buigzamer dan nylondraad. Spinzijde kan bovendien twee- tot viermaal zijn lengte worden uitgerekt voordat het breekt. Het is eigenlijk een soort superzijde, want zijderupsen maken eenzelfde soort eiwitvezel, alleen heeft die wat minder spectaculaire eigenschappen. De draad die uit het achterwerk van een spin komt, doet chemici en materiaalwetenschappers in ieder geval fantaseren over mensgemaakte varianten. En hoewel spinzijde een zeer complex bio-composiet is van diverse eiwitten, zijn er al tastbare successen. Het Duitse bedrijf AMSilk produceert een van de belangrijkste spinzijde-eiwitten (spidroïne) in bacteriën. Met dit eiwit maakt het bedrijf kunstspinzijde onder de naam Biosteel. In 2016 presenteerde Adidas een prototype hardloopschoen met een bovenwerk van kunstspinzijde. Het bedrijf claimde dat de schoen met een zakje enzympoeder binnen 36 uur oplost in water, en dan door de gootsteen kan worden gespoeld. Dat is heel circulair maar illustreert ook de kwetsbaarheid van eiwitdraad ten opzichte van aramide en polyethyleen.
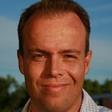
Nog geen opmerkingen